电磁线质量控制与绕组匝间故障分析
发布时间:
2023-02-21 10:08
电磁漆包线是电机绕组的主要原材料,必须满足导体形状和规格、高温下长期工作、高速下强振动和离心力、高压下耐电晕和击穿、特殊气氛下耐化学腐蚀等要求;制造工艺要求线圈能够承受缠绕和嵌入过程中的张力、弯曲和磨损,以及浸泡和干燥过程中的膨胀和侵蚀。避免电机绕组使用不合格的电磁漆包线是电磁线检测和控制的首要任务。因此,电磁漆包线的进货检验必须明确关键的监控指标和验收标准。在每个生产过程和运输过程中,都要注意加强保护,避免存在质量隐患的电磁漆包线缠绕顺序,降低匝间故障的概率。
1.电磁漆包线检测与控制主要指标。
电磁漆包线需要控制的主要指标是电磁漆包线的外形尺寸、机械性能、耐热性、电气性能、漆膜连续性和耐化学性。
1.1电磁漆包线外形尺寸的检查和控制。
电磁漆包线的尺寸检验主要包括线径允许公差、最大外径和最小膜厚。线径允许公差是指裸线直径的实际值与规定值之间的允许偏差,公差越小,越有利于设计过程中电阻、匝数等数值的计算。最大外径是导线允许的最大直径,最大外径的超差会增加线圈尺寸,增加槽填充率。最小膜厚是导线允许的最小膜厚。薄膜太薄,容易产生针孔,导致耐压性、耐擦伤性、耐化学性、耐老化性下降,导致电机绕组潜在质量问题严重。表1是不同直径漆包线各种参数的允许范围。
1.2电磁漆包线机械性能的检测与控制。
在电机线圈的缠绕和埋设过程中,缠绕时的拉力、摩擦力、弯曲力等机械力,埋设时的摩擦力,电机运行时振动引起的匝间摩擦都作用在绕组上。如果漆包线的芯线或漆膜达不到要求,机械力会给漆包线带来不同程度的损伤。漆包线绕成线圈主要受两种外力。一个是拉力。如果漆膜弹性不足,漆膜受力后的伸长率跟不上导体的伸长率,漆膜就会开裂。二、弯曲力,弯曲后外缘漆膜拉长,内缘漆膜压缩。弹性不好,漆膜会开裂。细线容易拉伸,用伸长法测试;粗导线受弯曲影响较大,所以采用缠绕法测试。电磁漆包线漆膜的耐刮擦性是用漆膜在一定外力作用下的耐刮擦次数或破断力来表示的,在线圈绕制、嵌线和电器产品运行过程中,会有压力或摩擦力作用在漆包线上。因此,电磁漆包线的机械性能测试是一项重要的测试项目。
1.3漆包线耐热试验。
漆包线的耐热性直接影响电气设备的设计和使用。电气设备的温升受漆包线等绝缘材料的限制。使用耐热性高的漆包线和配套材料,可以在结构不变的情况下获得更好的可靠性,或者在功率不变的情况下达到减少有色金属等材料体积、重量和消耗的节能效果。漆包线的耐热试验主要包括热老化试验、热冲击试验和热软化击穿试验。热冲击试验是研究漆包线膜在机械应力下的耐热性。耐热软化击穿试验:在线圈中,下漆包线受到上漆包线张力的作用。如果漆包线处于预干燥或浸渍的干燥过程或高温运行,漆膜受热软化,在压力下逐渐被挤薄,线圈可能产生匝间短路。
漆包线电气性能的检测与控制。
漆包线中的电流沿着线圈芯线循环,产生电磁感应,使电机绕组发挥作用。漆膜的介电强度达不到要求,线圈就会短路。介电强度的检验标准是电磁漆包线的最小击穿电压,不同直径的电磁漆包线的最小击穿电压见表2。
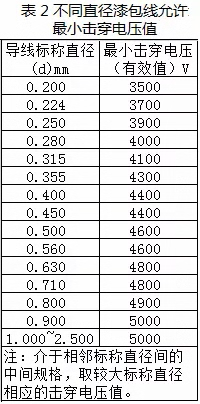
击穿电压是指在强电场的作用下,聚合物中束缚的电子从电场中获得能量,成为自由电子,向电场方向运动。当自由电子与运动中的其他束缚电子碰撞时,它们被激发成自由电子,这增加了聚合物的导电性。当电场强度超过一定值时,在聚合物中形成连接两个电极的孔道,使增加的电流通过,聚合物失去绝缘性能而被击穿。此时施加电压的强度称为击穿电压。当电压击穿时,热量会对聚合物造成热损伤,聚合物会熔化燃烧。影响击穿电压的主要因素有漆膜厚度和不圆度、固化程度、油漆中的外部杂质等。漆包线电气性能测试中,影响击穿电压测试数据的主要因素是捻度、电压施加时间、升压速度、漆膜伸长率和压力温度。
1.5漆膜的连续性和耐化学性。
对于中小型电机,分散绕组的电磁漆包线匝数多,绕组紧密,线与线之间接触面多。漆包线漆膜如果针孔多,两圈之间针孔重叠,会造成导线间短路。漆包线的耐化学性包括耐酸性、耐碱性、耐盐雾性、耐湿性、耐油性、耐溶剂性、耐制冷剂性、耐辐射性,一般由电磁线厂家控制。在线圈浸渍过程中,漆包线必须经过热震和软化击穿的热性能测试,还会受到浸渍漆中甲苯、二甲苯、石油溶剂和油等溶剂的侵蚀。不同的漆膜对不同的溶剂有不同的耐受性。浸渍时,应根据漆包线的特点选择适合漆包线的溶剂浸渍漆。
2.漆包线针孔的危害及检测。
漆膜的连续性是电磁漆包线的重要关键性能,在一定长度下漆膜针孔的数量必须在合格范围内。专业的漆膜连续性测试仪可以用来检查针孔的数量。针孔越少,电磁线漆膜完整性越好。利用高压放电原理可以检测针孔缺陷,电磁线与高压凹轮半包络接触。当膜厚不足或有严重的裸铜缺陷时,仪器会记录具体的缺陷编号。
漆膜出现针孔的原因可以归结为两种:一种是铜材不合适,成型的线芯有很多毛刺,可能是原材料本身或者拉丝工艺造成的;其次,喷漆不均匀、油漆中的杂质、油漆质量和喷漆后的干燥方法都容易导致电机匝间故障,影响电机的使用寿命。
目前大多数电磁线生产厂家应用的漆包线漆膜连续性在线检测系统是基于DC高压电场传感器的非接触检测方法。其基本原理是由DC高压电路产生DC高压,连接到高压电场传感器中的圆柱形金属导体,在圆柱形金属导体内部产生高压电场。漆包线在收线轮的带动下高速通过高压电场。当电场强度足够大时,漆包线表面会产生电晕。如果漆膜有缺陷的漆包线通过,金属导体、漆包线和收线轮之间会形成局部放电引起的漏电流。通过动态测量漆包线漏电流的变化,可以准确测量和记录漆包线的缺陷位置和严重程度。
用这种方法检测时,漆包线和传感器在整个过程中没有接触,不会对漆包线造成额外的损坏。非常适合生产线上高速运行的漆包线的在线检测。高压电场传感器中的金属导体近似圆柱形,产生的电场在各个方向上基本相同,因此各个方向的检测能力基本一致,检测灵敏度高。电机制造中的电磁线检测通常采用漆膜连续性测试仪,只能在半包络状态下进行检测,其发现缺陷的能力较弱。但由于采样的随机性,基本可以定性判断电磁线的性能顺从性。
3.油漆不足对电机性能的影响。
对于电机产品,浸泡干燥过程是关键控制环节,主要由工艺设备和工艺管理控制。电机绕组浸入式干燥是用绝缘漆将绕组内的所有缝隙填满,干燥后使绕组成为一个坚固的整体,以保证电机的绝缘、散热和振动性能满足要求,达到电机的综合性能水平。在拆卸有绕组故障的电机时,发现绕组松动,对电机的性能有很大的不利影响。
为了在电机绕组上获得充分有效的油漆涂层,应注意浸泡和干燥过程中涉及的材料、工艺参数和工艺控制。油漆的粘度在浸渍过程中非常关键。如果油漆太薄,就没有足够的油漆填充绕组中的间隙,油漆太厚就无法进入绕组,尤其是铁芯槽中。利用VPI真空压力设备进行浸漆,可以有效提高浸漆效果。在实际生产过程中,必须动态监控浸漆设备的状态和油漆的粘度。在绕组绝缘处理过程中,大多数浸渍和干燥过程是分开进行的,浸渍前的预干燥可以去除绕组中的水分和空气。浸渍后烘干,烘烤温度低的话,已经进入绕组的油漆会流失,绝缘处理效果不好;如果温度过高,会造成电磁线、绝缘等材料老化失效。对于大多数干燥过程,绕组处于静止状态,会导致绝缘漆相对于绕组分布不均匀,绝缘漆固化时间过长,会增加对绝缘处理的不均匀影响。为了提高绕组的绝缘处理效果,烘烤设备可以增加旋转处理功能,保证绕组在干燥过程中处于旋转状态,从而有效提高绝缘漆在绕组中的分布均匀性。
根据绕组加工工艺,在浸渍干燥过程中应尽可能增加绝缘漆的填充量,以保证浸渍干燥效果。设备的选择、绝缘漆的性能参数、工艺参数和工艺执行程度是生产加工过程控制的重点。
4.结论。
在电机制造过程中,绕组、埋设、接线、运输和组装可能会对电磁线绝缘层造成损坏,从而导致电机测试或实际运行中的匝间故障。除了生产加工对电磁线造成的损伤因素外,电磁线本身的质量性能也非常关键。电磁线绝缘层的附着力、绝缘层的均匀性和导体的光滑度直接影响电机绕组的可靠性。对于成型绕组,在线圈拉制过程中,对电磁线绝缘层的机械强度要求较高,质量差的电磁线往往会出现绝缘层损坏,导致匝间绝缘严重失效。设计过程中电磁线的选择、缠绕加工工艺的满意度、加工过程中电磁线绝缘层的保护是电磁线降故障控制的关键要素。电磁线在制造过程中损坏的部分是电机运行过程中的质量隐患。在电机启动过程中,绕组中直接与电源相连的第一个线圈受到的冲击最大,在电机绕组的嵌入过程中,线圈往往变形最严重。通过对实际故障案例的检查,发现无加强措施的电机绕组匝间故障多发生在第一匝。特殊的绝缘措施可以有效减少绕组匝间故障。
相关新闻